Global July 16, 2023 - By
For Mohammed S. Alduhaimi, his work in the Refined Products Division of our Oil Supply Planning and Scheduling Department is all about concentration and the ability to react swiftly and properly.
The Arabian Sun spent the day with Mohammed S. Alduhaimi, an engineer in the Oil Supply Planning and Scheduling’s (OSPAS) Refined Products Division (RPD), to understand more about their mission to deliver energy optimally and reliably.
Every morning before starting work at 6:30 a.m., Mohammed S. Alduhaimi goes to the gym.
“It helps me clear my mind and prepare for the day ahead,” he says.
It’s easy to understand why he does this, Alduhaimi’s job as an engineer in the Oil Supply Planning and Scheduling’s (OSPAS) Refined Products Division (RPD) requires nonstop concentration and the ability to respond quickly to any issues that may occur. It is high-pressure from the moment that he walks into the office.
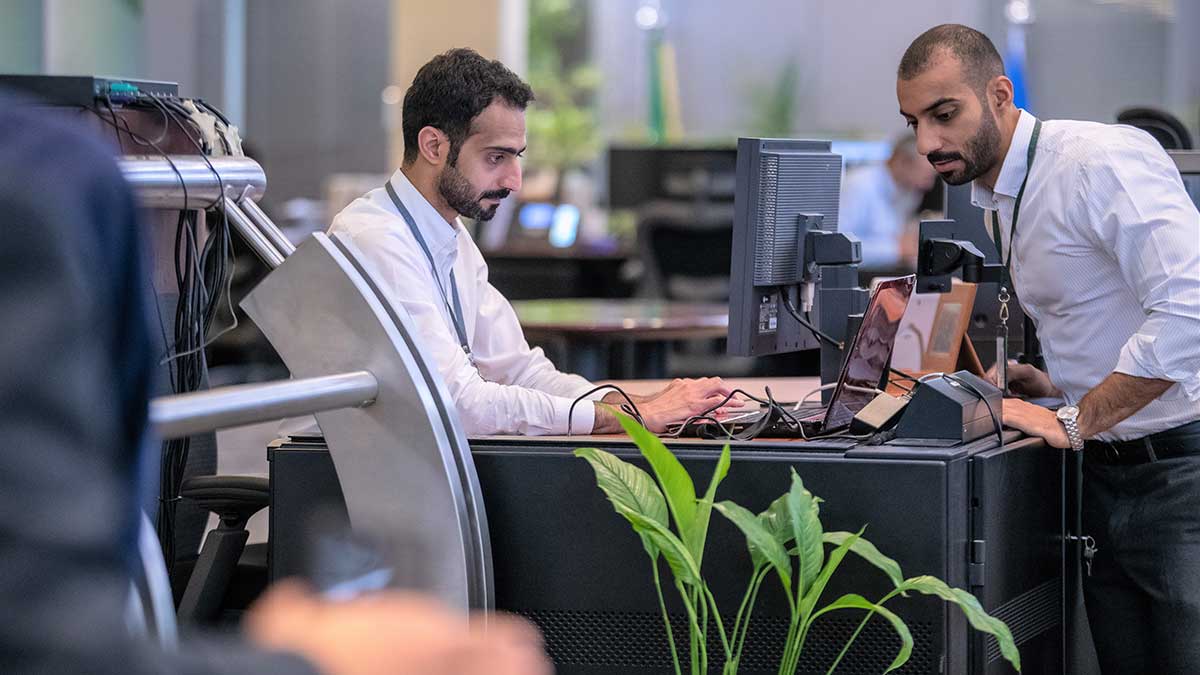
‘There is no room for error’
Alduhaimi starts his day by reading through a series of reports that are automatically generated overnight. They give an insight into the performance across the entire RPD system, which includes numerous bulk plants, refineries, and export terminals.
If there are any issues that need immediate action, Alduhaimi and his colleagues need to first understand what has happened. A contingency plan would then be activated to maintain the reliability and resilience of the hydrocarbon supply until normal operations are restored.
We have to act immediately … our job is to get things back on track.
— Mohammed S. Alduhaimi
OSPAS consists of four operational divisions, the Oil Division, the Gas and NGL Division, RPD, and the Terminal Planning Division, and three support divisions, the Supply Planning and Optimization Division, the Planning and Support Division, and the Corporate Emergency Management and Continuity Division.
All of them play a critical part in OSPAS’s mission to deliver premium hydrocarbon products timely, optimally, safely, and in an environmentally responsible manner to local and international customers. This is done through the talent of its people who leverage state-of-the-art technology to maintain the resilient system and achieve maximum revenue realization.
“Everyone in OSPAS has the mentality that there is absolutely no room for error.
“We have to do what we need to do to make sure that energy is delivered reliably and safely both to customers in the Kingdom and internationally,” Alduhaimi says.
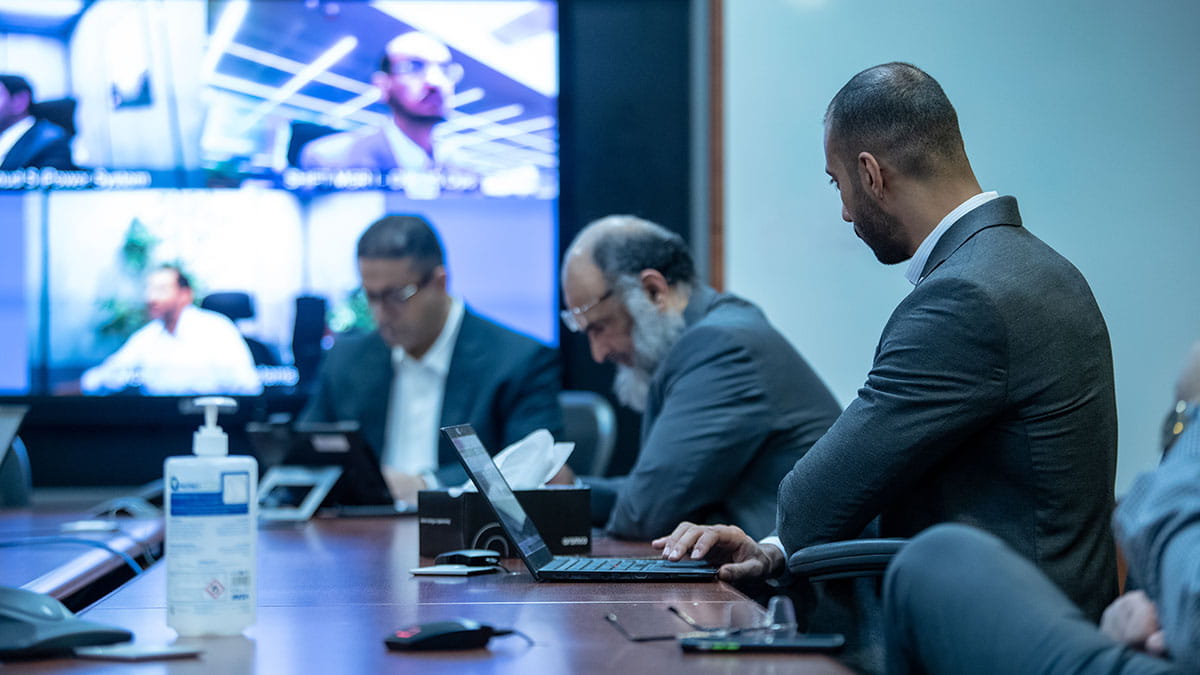
Communication key in OSPAS
There is a high-level call at 7:05 a.m. every morning, led by OSPAS vice president Mohammed H. Al Ghamdi and often listened in to by executive management.
Typically, facility directors and shift managers from every hydrocarbon facility in the Kingdom reports on performance and whether there are any upcoming issues that OSPAS needs to be aware of.
“It’s a short call but a very important one that makes sure everything is safe across the network and if there’s anything that needs to be known about for OSPAS’s support,” Alduhaimi says.
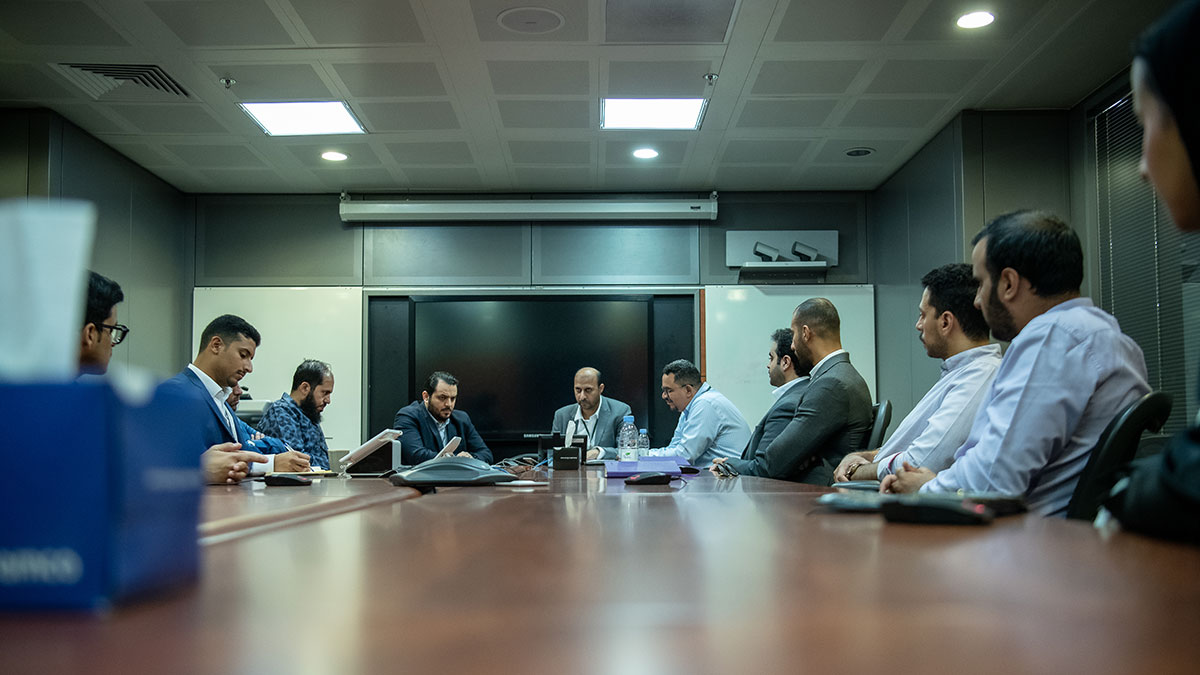
This broad overview is then followed up by several calls, which go into more detail — including the RPD meeting at 8:30 a.m. This meeting usually lasts around 20 minutes, but once it is finished, the engineers will have all of the operational matters reported across the Kingdom’s refining system over the last 24 hours.
They will then leave no stone unturned as they start analyzing data and adjusting the daily supply plan to ensure that the division’s Short-Range Operating Plan (SROP) — the monthly plan that OSPAS follows to meet its energy commitments — is being adhered to.
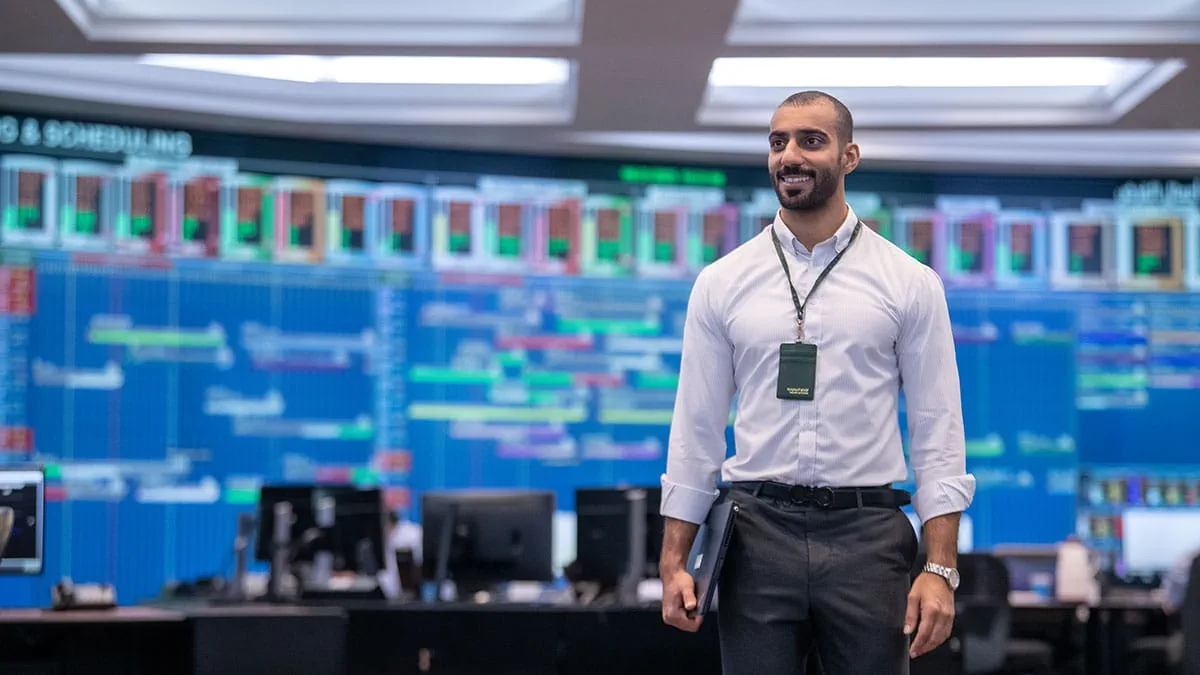
The role of technology
Alduhaimi and his colleagues now use an in-house designed software program, which automatically gathers all of the data needed to generate an optimum supply plan, which has saved the division countless man-hours.
“Previously, we looked at the SROP, manually looked at the data, the demand, the refineries’ production — migrate all of this information into an Excel sheet — and then set the daily optimized RPD supply plan,” Alduhaimi says. “Now, this is all done automatically. The software even generates a report for you and gives you the most optimal plan of what you need to do; previously, this was done manually.
“It took two years to build because of the sheer amount of data points involved, but it has saved a lot of time.”
The advancement of technology in OSPAS in recent years has allowed engineers to focus even more on digital transformation and automating processes.
“The numerous projects that we’ve accomplished to automate and optimize our processes have saved a significant amount of time. We can now focus more on important things like digital transformation,” Alduhaimi says.
“We now have the time to focus on developing software tools and understanding how to use existing tools, which is then reflected in our operations.”
There is more to come with the OSPAS team exploring how the latest technology, such as artificial intelligence, machine learning, and robotics, could further improve the division.
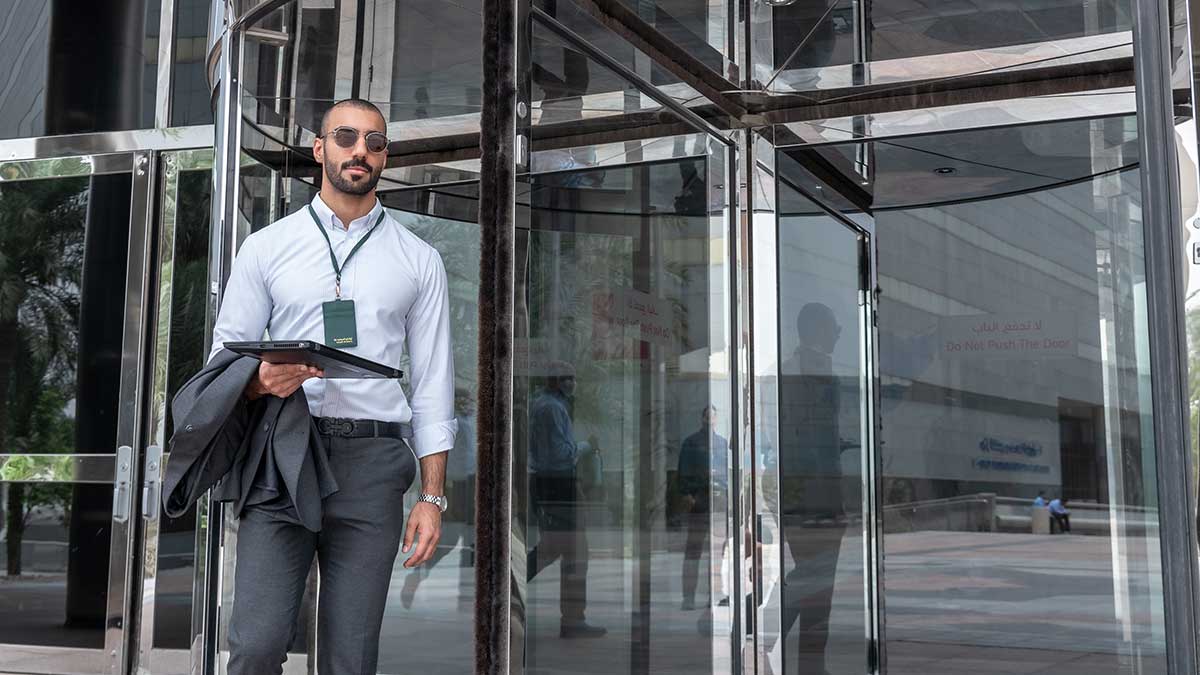
Meeting KPIs
Another important component in Alduhaimi’s role is monitoring key performance indicators (KPIs) to ensure that OSPAS is delivering energy in an optimal and reliable way. Performance reports have now been transferred into a modern, efficient, and user-friendly dashboard, which can even be accessed on smartphones via secured application, that will allow you to check things such as crude delivery to terminals or inventory levels.
“The latest technology has definitely made things easier for us, and helps us to respond quickly to any issues. There is no room for error, especially for the corporate reliability KPIs, because this is what Aramco is famous for — its reliability,” Alduhaimi says.
Before leaving for the day, Alduhaimi will often help with the daily check on the Emergency Monitoring Room (EMR) — which is used when there are serious incidents — to ensure that it is working optimally. Those in the EMR have access to live video streams and aerial views of facilities across the Kingdom, as well as an online messaging service and radios to keep in touch with key individuals on the ground.
He will then handover to the afternoon shift and inform them of any work that needs to be carried out.
It is a busy and often nonstop day, but Alduhaimi knows the importance of the work that he and his colleagues carry out.
“We have a huge sense of pride and responsibility within OSPAS, and an understanding of the magnitude of the work we carry out,” he says.
“We know that we don’t just have to do our day-to-day jobs perfectly, but also go above and beyond to be top-of-the-class in every way.”
Caption for top photo: Mohammed S. Alduhaimi and his colleague check a screen in the Emergency Monitoring Room, which is used when there are serious incidents. (Photos by Hatim B. Oweida/MPD)