3D Building
3D-printed building constructed in Hawiyah
Construction printing is an ideal digital solution in meeting our capital projects program demands while using minimal resources.
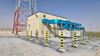
Aramco’s first 3D printed concrete industrial building has been constructed in Hawiyah.
Project Management (PM) at the company’s Hawiyah Unayzah Gas Reservoir Storage (HUGRS) Program and Consulting Services Department (CSD) led the innovative construction work, which is all part of the company’s pursuit to be a global leader in digital innovation in the energy sector.
.
Additive manufacturing, also known as 3D printing or 3D construction printing (3DCP), has emerged as an ideal digital solution for satisfying the demands of Aramco’s capital projects program while minimizing the resources required — meaning it is in line with the company’s commitment to decarbonizing its operations.
First 3D concrete printed industrial building
The 3D printed radio shelter building stands at a height of 3.85 meters and has a 63-m2 footprint. The construction required modifications to ensure that it had fully reinforced walls.
The building was completed in record delivery time with a printing speed of 100 millimeters per second. The stationary machine had a printing capacity of 7 meters width by 4 meters length by 4 meters height.
The automated nature of 3D printing also reduced the risk of glitches and delays.
With continuous printing across the day, delivery times can be accelerated by more than 45% compared to conventional construction methods. It also helps with reducing costs thanks to savings of up to 60% on used building materials and up to 80% on manpower.
Other advantages of this technology include:
- Construction waste reduction
- Lower risk of injuries and fatalities from the reduction of manual labor
- Reduced chance of human errors.
The radio shelter work was carried out with the collaboration of HUGRS program contractor Samsung Engineering.
How 3D concrete printing works
Slicing software first takes the designers’ structural models and formats them in a way that 3D printers can understand.
The process of concrete printing involves layering strips of mortar by using automated equipment to create 3D structures. A cantilevered arm-type printer was used for the radio shelter construction.
The 3D printing market is gathering momentum and is projected to play a major role in the developments in industrial and construction sectors envisioned in Saudi Arabia’s Vision 2030.
Aramco’s 3DCP Program
PM and Engineering Services are spearheading the company’s initiatives for developing and implementing 3DCP in Aramco.
A three-step approach has been adopted to achieve developing the expertise, streamlining deployment, and promoting localization.
• Developing the expertise: The team has identified and engaged with 21 international technology providers to understand their capabilities. This has led to selection criteria and deployment opportunities being developed.
• Streamlining deployment: After developing multiple proposals and conceptual designs, the one-story radio shelter building for the HUGRS program in Hawiyah was constructed ahead of all other propositions.
• Promoting localization: Wa’ed and Mighty Buildings (MB), a U.S.-based startup company specializing in the manufacturing of 3DCP prefabricated modular transportable homes, have secured an agreement, which includes MB’s localization within two years.
Caption for top photo: Aramco’s first 3D printed concrete industrial building has been constructed in Hawiyah. The radio shelter work was carried out with the collaboration of HUGRS program contractor Samsung Engineering