Hawiyah Gas Storage
VIDEO: Powering Saudi Arabia’s summer with gas
The video is blocked
By December 22, 2022
Hawiyah gets ready to launch Kingdom’s first underground gas storage.
At the midpoint of the world’s largest onshore oil field, Ghawar, natural gas will be brought to the surface, processed, and then returned underground to one of the field’s depleted gas reservoirs, Unayzah.
Why go to all this effort, only to put the gas back underground? Lowering the Kingdom’s domestic energy carbon emissions is a key reason.
Storing sales gas helps to ensure gas powers Saudi Arabia’s domestic electricity supply during its seasonal power consumption months. The Kingdom’s domestic power demand peaks in its summer months, but drops significantly in the winter months.
Another key reason is business-related. Processing the gas increases production of highly valuable byproducts such as ethane, condensate, and natural gas liquids (NGL).
Hawiyah gas storage plant commissioned
Two orderly lines of steel pipes, tanks, vessels, pumps, and enormous compressors tower above rose-gold desert sands in Saudi Arabia’s eastern region. While the methodical infrastructure of both appears identical, the eastern line injects gas, while the western line produces gas.
Together with associated utility infrastructure, they collectively comprise Saudi Arabia’s first subsurface sales gas storage facility, Hawiyah Gas Storage (HGS) plant, whose purpose is to compress sales gas for injection underground, storing the gas until it is needed.
When required, HGS can provide up to 2 billion standard cubic feet per day of sales gas for reintroduction into the Kingdom’s Master Gas System (MGS), an extensive network of pipelines connecting Aramco’s key gas production and processing sites with customers throughout the Kingdom.
By the summer of 2024, during peak domestic gas demand time, the site is scheduled to commence reproducing the same stored gas for reintroduction back into the MGS.
Raising gas production and storage capacity forms a fundamental part of Aramco’s long-term growth strategy. Our Hawiyah facility not only positions us as a leading force in energy transition, but simultaneously unlocks our strong ambitions for chemicals and low-carbon hydrogen while facilitating a new wave of Saudi industrial growth.
— Nasir K. Al-Naimi, Upstream senior vice president
HGS development head Bader Jughaiman said the project was executed in a record 45 months from design to construction, “Despite the unprecedented COVID-19 pandemic, and the accelerated schedule, the project team’s resilience and agility were key enablers in this success.”
“The integrated project team developed and implemented a business continuity plan to ensure design, procurement and construction activities were not impacted, such as overcoming travel restrictions by conducting all design reviews and equipment testing through digital platforms,” he said.
“Aramco engineers from different countries around the world gathered in hundreds of meetings reviewing the design and testing equipment remotely utilizing latest technologies, and implemented a risk-based approach in procuring materials to mitigate the supply chain disruption.
“An onsite COVID testing and monitoring system was established to prevent the spread of cases among the construction team, keeping people safe and avoiding impacting the project schedule,” Jughaiman added.
Designing and constructing a facility of this magnitude in 45 months is a testament of Aramco’s excellence in project execution.
— Khaled A. Al-Buraik, Southern Area Oil Operations vice president and project sponsor
Unayzah reservoir life extended
Oil and gas trapped in an underground field accumulates in potentially multiple spaces known as reservoirs. The depleted Unayzah nonassociated gas reservoir, located in the Ghawar field’s Hawiyah production area, was a prolific gas producer for decades.
Technical and economical assessment identified Unayzah’s excellent parameters as suitable for a subsurface structure, and it was decided to further leverage the reservoir’s life by extending its service into underground sales gas storage.
Unayzah’s assessment included using GigaPowers to integrate a wide range of static and dynamic downhole surveillance data with the most recent drilling results, and Gas Reservoir Management Department manager Adnan Al-Kanaan said, “The sales gas storage project is a concrete example of our pursuit of innovation and drive for growth and excellence.”
Multi-skilled wells
HGS’s 22 wells need to inject for six months during the winter, and produce for six months during the summer, so each wellhead has a dual set of flowlines. Twelve of Unayzah’s dormant production wells were retrofitted with overhead injection equipment, while 10 new wells were drilled.
Underbalanced coiled tubing was used to drill Unayzah’s new wells. ‘Big bore’ well completions resulted in doubling the injection and production rates per well, also reducing the number of wells required.
The project team moved beyond traditional project execution by adopting smart execution techniques, and best design practices to successfully steer the program in delivering the first Kingdom gas storage at large scale.
— Abdulkarim A. Al-Ghamdi, Project Management vice president
Southern Area Production Engineering Department manager Mohammed A. Atawi said rigless activities were used to evaluate both reservoir and well conditions, “Being able to lead the execution and evaluation of such comprehensive rigless activities in parallel to the vast project construction work exemplifies the team’s strong planning and dedication.”
Exceptionally high pressure
Aramco is no stranger to high-pressure gas. Putting gas back into a reservoir requires a lot of compression, and HGS’s 32 compressors are among the most powerful at Aramco.
Moving high-pressure gas for injection into a reservoir requires exceptionally tough piping. Aramco conducted a world-first integrity test to operate, for the first time, a high-pressure gas pipeline from HGS to the gas gathering manifold, and finally the 22 wellheads for injection.
This initiative is instrumental in effectively meeting energy demand as it provides a contingency tool to supply gas upon need.
— Waleed A. Al-Mulhim, Petroleum Engineering and Development executive director
During the first half of 2022, HGS’s chosen pipeline material was simulated to its operating conditions in Italy, and tested for its integrity to withstand 6,000 pounds per square inch. The full-scale fracture propagation tests conducted confirmed the ductility of the chosen pipeline material, and ability to arrest the progress of any induced cracks.
To enhance reliability and safe operations, HGS’s approximately 30,000 pieces of equipment are equipped with advanced analytics, and machine-learning technology. On the horizon is a digital twin, and first-time installations of a wifi gas detector, as well as a gas leak sonic detector to check on any gas passing to the flare system, while, hidden quietly on the site’s northern edge, is the radio shelter whose building was constructed using 3D printing technology.
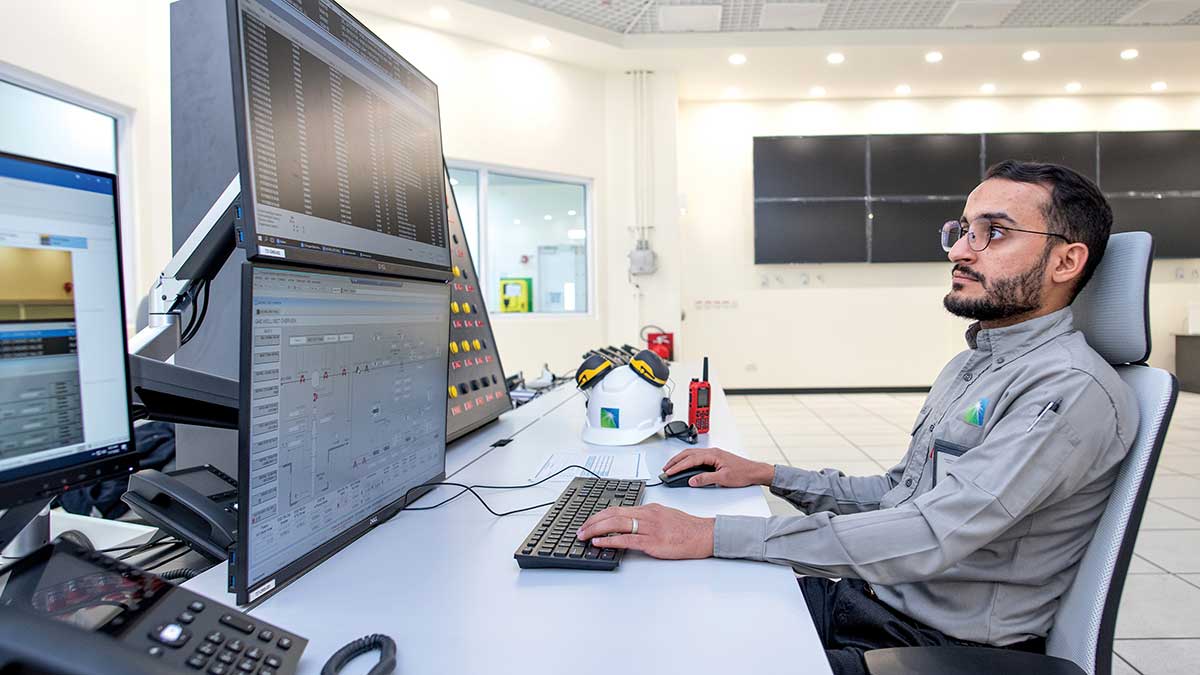
Technology monitoring instrumentation
Maintenance technician Ayman M. Alhajji, after obtaining a diploma in engineering technology, was accepted into Aramco’s industrial training program, and graduated from instrumentation in 2019.
Technology in oil and gas plants enhances safety, efficiency and mitigates greenhouse gas emissions, and part of Alhajji’s role is ensuring all HGS’s monitoring instrumentation is both working, and under control.
“Our vision with storing the gas is to reduce carbon emissions to help keep our environment healthy for our generation, and our next generation,” said Alhajji whose experience includes working with gas in the southern oil fields, and time at Abqaiq Plants.
Totally different operation
“Things are totally different here from all aspects,” said console operator Abdullah E. Alharbi.
“The facility will be operated in cycling mode for six months injecting gas into the reservoir and the other six months reproduction,” he said.
Alharbi, who trained as an operator with Aramco’s Industrial Training Center, holds seven years gas production experience — three years as an outside operator, and four years as console operator, and is now a certified trainer at HGS.
“I am helping to provide guidance for our younger workforce in how to check the gas wells, the trunklines, and control the system under all operational scenarios,” said Alharbi, whose part-time study saw him recently graduated with a Bachelor of Law from Imam University.
Learning from startup
Outside operator Saad H. Dossary holds seven years’ experience compressing sales gas at Hawiyah Gas Plant (HGP).
Dossary trained at Aramco’s own Industrial Training Center and brought to HGS his in-depth and hands-on experience. He has been instrumental in writing manuals for the site’s operating procedures.
He says there are immense benefits from working on a new facility, “It is good to be here from zero as it is a good chance to learn, and you acquire a lot of knowledge from the vendors and contractors about a safe startup.
“Being here from the start means you get to know the plant intimately, and are familiar with all aspects of running the facility to the best standards.”
The HGS program is testament to the successful accelerated execution efforts of Project Management and various Aramco organizations.
— Abdullah A. Al-Sughaiyer, Upstream Gas Project Management general manager
Accelerated learning curve
Compression dominates at HGS, and commissioning engineer Mohammed O. Alsulmi looks after 10 compressors.
The 2020 KFUPM chemical engineering graduate, with a one-year development assignment in a gas plant, says he is always learning something new at HGS, “The learning curve is accelerated as everything is dynamic and, challenges are tackled on a daily basis.”
“As a young engineer, I’m delighted to work in an accelerated project serving the company’s strategic ambitions,” said Alsulmi.
“I have been empowered to make critical decisions, hold meetings with several parties, lead and work with a team in order to achieve the aggressive project schedule.”
Caption for top photo: Abdullah E. Alharbi (right) and Mohammed O. Alsulmi on the job in Hawiyah.