The Aramco Hydrocarbon Journey
NGL: Decades of greenhouse gas mitigation in our operational DNA
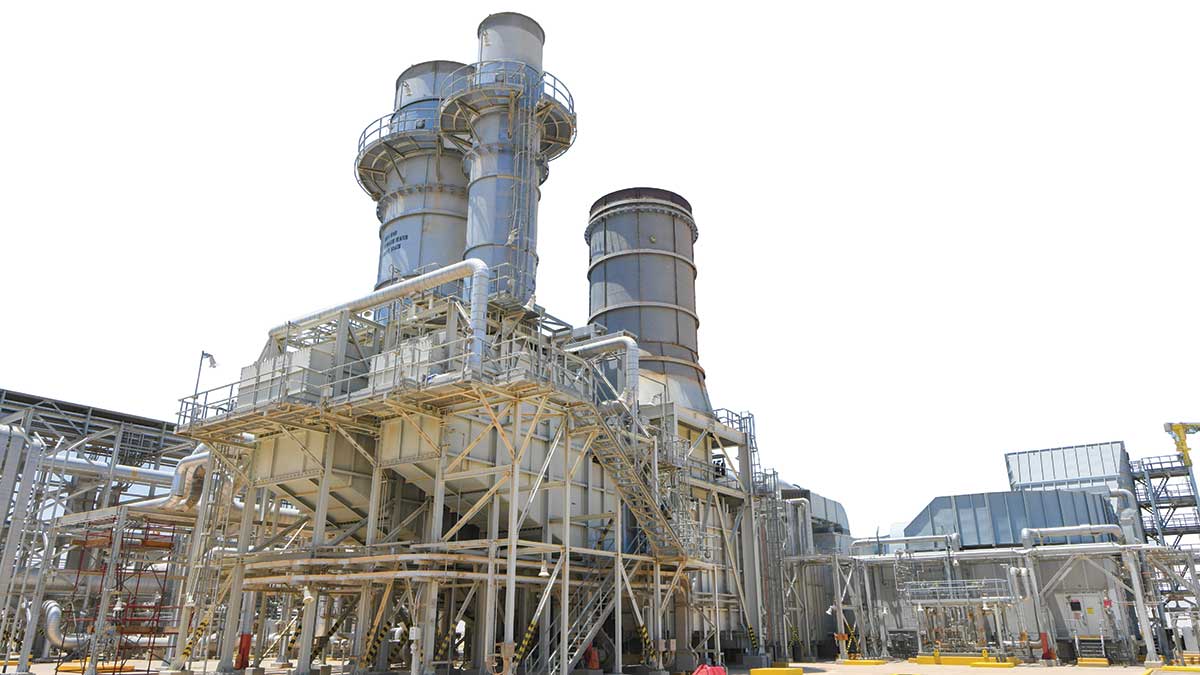
By November 17, 2021
Natural gas liquids (NGL) are key raw materials for chemicals and vehicle fuel blends.
Natural gas liquids (NGL) are highly valued components of natural gas, which are separated out in the form of liquids, and are key raw materials for chemicals and vehicle fuel blends.
Separating a hydrocarbon’s molecular chain is seemingly an endless voyage of discovery.
Among the processes used to peel back a hydrocarbon’s layers are gravity, heat, pressure, chilling, or by a catalyst. Remarkably, when these techniques are applied even further, a hydrocarbon keeps on giving generously.
Valuable natural gas byproducts
Natural gas is much more than methane. Applying the processing techniques of soaking or chilling to gas, reveals its concealed natural gas liquids (NGL).
Saturated with ethane, propane, butane, isobutane, and natural gasoline (pentanes plus), NGL are highly valued fluids for their wide applications — from specialized fuels, fertilizers, to petrochemical feedstocks.
Giant desert freezer
About an hour’s drive west of al-Hasa’s palm groves and oasis, a solitary steel forest of pipes and tanks rises quietly from the ad-Dahna desert’s baked sands.
The Hawiyah NGL plant, built in one of the hottest parts of Saudi Arabia in 2008, is essentially a giant freezer for gas.
A job of the chilly titan’s three NGL trains is to extract NGL from gas received from the nearby Haradh and Hawiyah gas plants.
Extraction is achieved by bringing the temperature of the gas down to a frigid minus 110 degrees Celsius.
After the freezing, leftover sales gas is sent directly to the Master Gas System customers, while the NGL goes to Shedgum for feeding to various fractionating plants.
The fractionating plants separate out ethane for industrial customers, while the remaining streams are fractionated into valuable liquids.
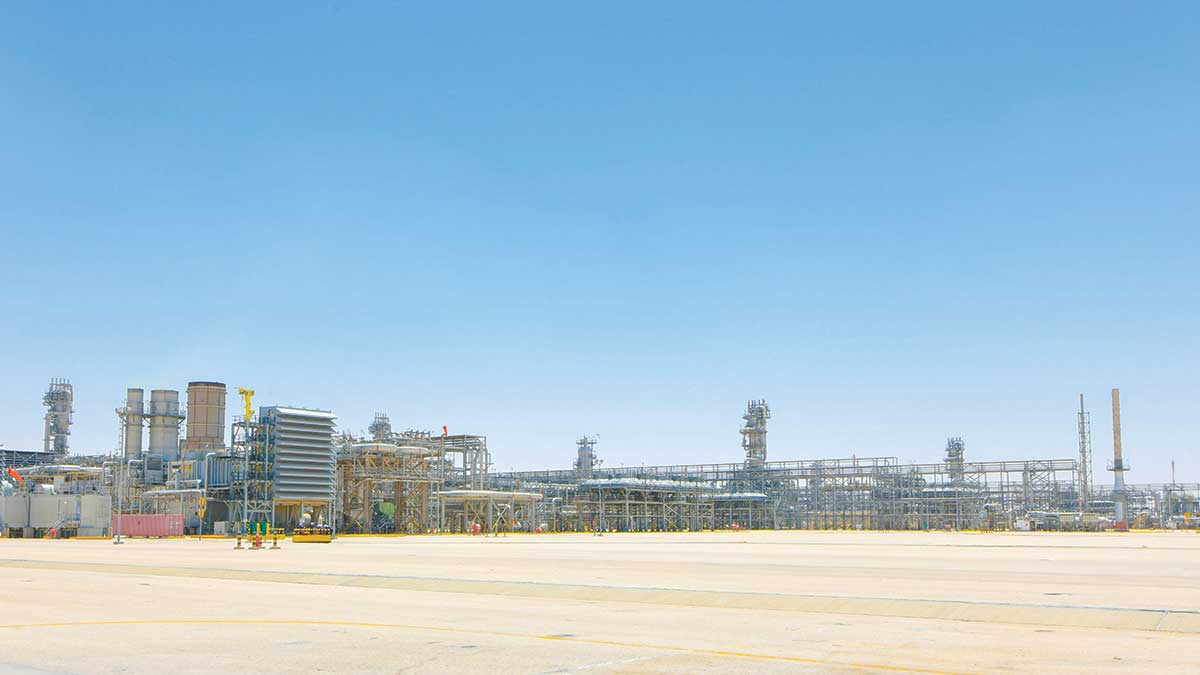
Industrial energy efficiency
Reductions in flaring and greenhouse gas (GHG) emissions can be achieved when industrial plants are efficient in the production of energy.
Prominent at most Aramco oil and gas plants is the whir of gas turbines, creating power for machinery like generators, pumps, compressors, and processing trains.
Reducing GHG emissions from gas turbines, and increasing their operational flexibility, are among key ongoing Aramco operational targets.
Four gas turbines mechanically drive four giant sales gas compressors at the Hawiyah NGL plant, and their power is generated by flowing air through an engine, pressurizing it, and feeding it to a combustion chamber at speeds of hundreds of kilometers per hour.
Energy is then added by spraying fuel gas into the air and igniting it to generate a high temperature flow, causing turbine blades to spin, which drive a compressor that converts the kinetic energy into pressure.
Aramco NGL infrastructure
NGL recovery straddle plants are at
Hawiyah NGL
Shaybah
‘Uthmaniyah
NGL fractionation plants are at
Ju’aymah
Yanbu’
Ras Tanura
Wasit
Digitization improving air, heat, and fuel mixes
In “lean-lean” mode, a combustor’s two primary and secondary zones have an actual flame, whereas in the “premix” mode, only the secondary zone has a flame.
“Premix is where the air and fuel are thoroughly mixed before combustion,” says outside operator Omar N. Almodrhim, who joined the Hawiyah NGL plant in 2012 after training for 18 months at Aramco’s industrial training facility in al-Hasa.
In 2017, Hawiyah installed new software to get the best out of its premix. Now, from inside the plant’s central control room, where all facilities are monitored 24/7 in real-time, the premix switch is done with the mere push of a button.
Using a digital helping hand to smartly switch the air-fuel formula from “lean-lean” to “premix” means gas flaring and de-loading are no longer required, therefore, achieving a reduction of nitrous oxide (NOx) and carbon monoxide emissions, as well as less need for maintenance, and higher availability.
“Introducing fuel gas to the first zone, before it is actual flame in the second zone, is better for the environment as its combustion products produce less NOx,” adds Almodrhim.