The Aramco Hydrocarbon Journey
Maintenance: Decades of greenhouse gas mitigation in our operational DNA
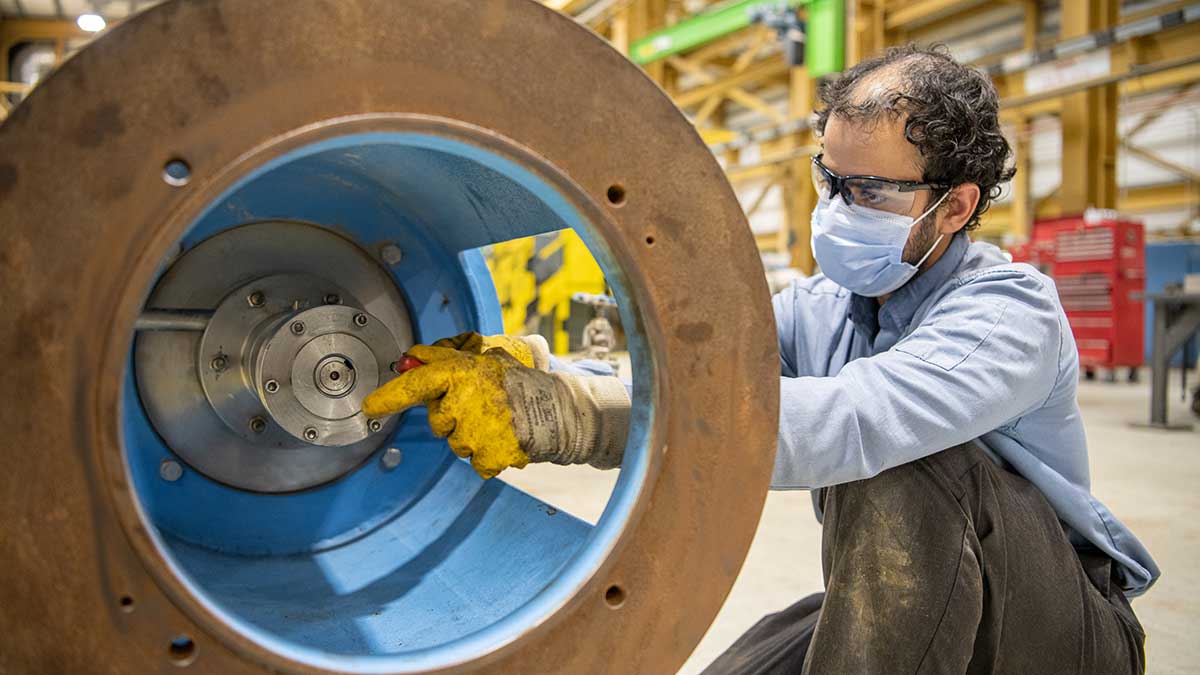
By November 03, 2021
At Abqaiq Plants, the largest stabilization plant in the world, maintenance plays a key role in sustaining a steady flow of fluids, ultimately equating to an avoidance of unnecessary greenhouse gas emissions.
At Aramco, decades of maintaining the efficiency and reliability of an extensive portfolio of assets has evolved into a finely calibrated orchestral performance.
This performance is delivered on a grand scale at Abqaiq Plants, the largest crude oil stabilization plant in the world. Well-maintained oil and gas facilities sustain a smooth and steady flow of fluids, which ultimately equates to avoidance of unnecessary greenhouse gas (GHG) emissions.
Operational issues leading to production interruptions, such as fluids not flowing through pipes or equipment breakdowns, eventually result in heavier carbon footprints, and environmental impacts.
Investing time and thought into keeping equipment and systems in their best readiness is better for the environment, as well as supporting business continuity.
Well-oiled chain of command
To deliver a best-in-class reliable production performance, everyone needs to know their part.
One maintenance department, five divisions, 25 units, and two workshops keep Abqaiq’s oil processing, natural gas liquids (NGL), and utilities facilities running smoothly.
A collective team of more than 500 people work to an extensive list of maintenance methodologies and processes — preventative and periodic, predictive or condition-based, repair, major inspections, overhaul, materials planning and procurement, reliability, and arguably the ultimate maintenance activity, test and inspection.
Alongside the well-tuned organizational hierarchy, is nifty thinking about the convergence of new and old equipment, and technology.
Fusion of new, old, and technology
Abqaiq Plants sparkles with the latest equipment, smart digitization, and some maturing, but sturdy, assets.
It takes an abundance of fixed and rotating equipment to move, steam, and compress vast quantities of fluids, all needing to remain contained in their pipes and vessels. To uphold quality, performance, and avoid damage to other assets, each piece of Aramco production equipment has its own personalized maintenance history and plan.
Vast amounts of data are gathered on Aramco equipment; its classification, downtime, behavior, intervention history, spare parts, and when an issue requires escalation, the inspection team is mobilized to troubleshoot the issue.
Sturdy seniors
Thanks to maintenance, the older equipment continues to operate on the front line with astounding reliability. However, aging assets have their challenges, such as finding replacement parts.
Single shaft gas turbine “KT-501,” tucked among the youngsters in the NGL plant, has stoically served gas compression train 334 since 1968. Since its commissioning in 1968, the sturdy turbine has clocked approximately 299,500 run hours, and holds the awesome title of the only piece of equipment of its kind still operating in Saudi Arabia.
The manufacturer, so impressed by its service at Abqaiq, has requested to display the turbine, once retired, in their own facilities.
Innovative mitigation
Gas from the oil is compressed by Abqaiq’s NGL facility in eight compression trains, passed through the stripper columns and deethaniser column, producing NGL for Ras Tanura, and light gases for further processing at other plants.
Driven by seven gas and one steam turbine — with one gas currently being replaced with steam — the continuous operation of gas compressors is critical toward minimizing flaring. Changing a turbine’s fuel from gas to steam is a significant mitigation investment.
The utilities facility supplies both the oil and NGL with power from three generators, and lost energy from exhausts, in the form of wasted heat, is captured through a cogeneration system.
To increase energy efficiency, exhaust linings in all cogeneration units were recently replaced. In an Aramco first, Abqaiq reverse engineered a mature, functioning but obsolete, steam turbine rotor. After disassembling the turbine, its equipment was scanned, and the online blueprints can now be used to manufacture spare parts to lengthen its lifespan even more.
Human-centered digitization
For oil and gas production, there is no room for mistakes in asset integrity, and automation provides a helping hand toward GHG emission reduction.
Just as big as Abqaiq Plants, is the welcoming thinking about technology by its maintenance people.
“Greenhouse gas mitigation is essential to preserve the environment for future generations,” says maintenance engineer Saad K. Alharbi, who holds a mechanical engineering degree from Colorado School of Mines, U.S.
Sensor networks on equipment keep a 24/7 monitoring watch to help an equipment’s life cycle, pending failure, and its optimal maintenance period.
Alharbi says being able to self-manufacture discontinued parts is extremely useful. “This is supported by examples of manufacturing parts for vibration sensors and other aging infrastructure.
“3-D printing technology reduces maintenance miles and may be used to manufacture parts,” he added.
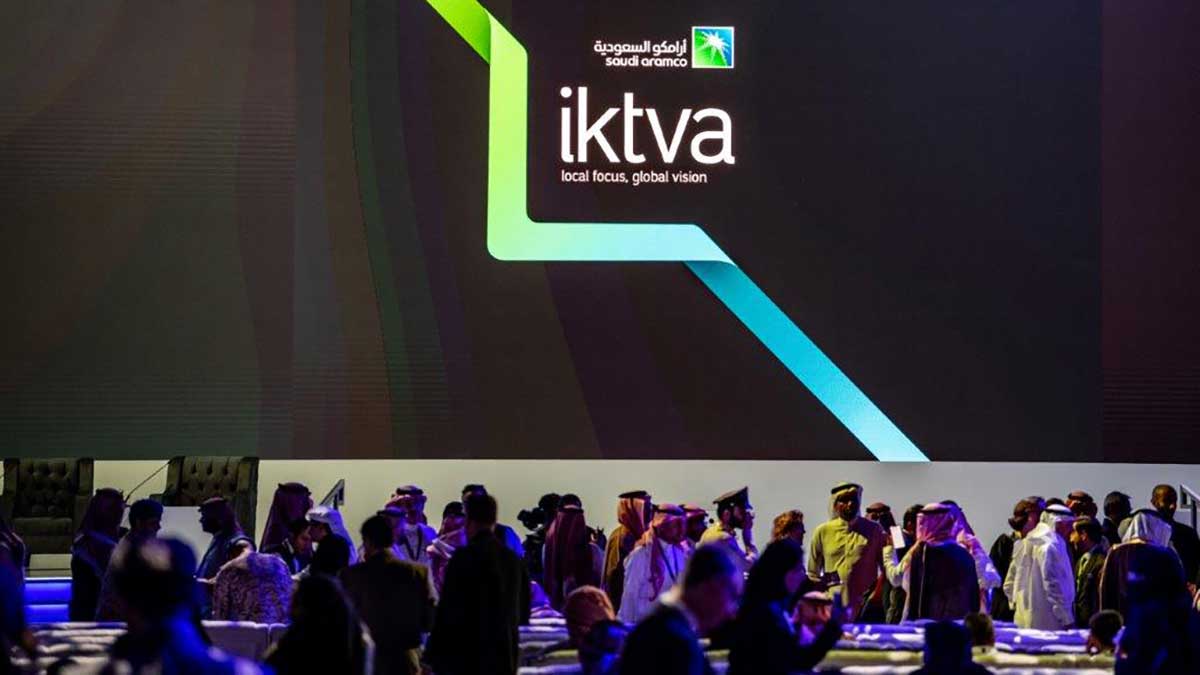
Reducing maintenance supply miles
Localized supply chains, generally, mean lighter footprints, and enables Aramco to maintain operations with minimal disruption.
Through its In-Kingdom Total Value Add (iktva) program, Aramco is actively building a world-class supply chain, with the goal to retain 70% of all procurement spend in-Kingdom.
The 2020 Saudi Aramco Annual Report shows that the company's percentage was 55.8% in 2019, which then increased to 57.5% in 2020.