By October 06, 2021
Decades of greenhouse gas mitigation in our operational DNA.
Gigantic reddish-brown sand dunes tower above field operator Abdullah R. Fadly, who walks purposefully from his vehicle to a remote desert pipeline junction station.
Early morning dry heat shimmers across the imprints of his black steel-capped boots as he and his colleague set out to commence a routine check of Shaybah oil field’s “kilometer 9.8” pipeline junction site, as well as other junctions scattered along pipelines stretching 645 kilometers (km).
In Saudi Arabia’s grand Rub’ al-Khali (Empty Quarter) desert, the world’s largest expanse of sand, nature’s awesome grandeur, and arid climate are on striking display at Shaybah.
Unforgiving climate
The desert is Fadly’s workplace — a ruthless place for the inexperienced. Hiis role, driving long distances to check crude and natural gas liquid (NGL) pipelines, demands particular self sufficiency and adaptability.
He is one of Aramco’s pipelines team members across Saudi Arabia ensuring a trouble- and emissions-free journey for the piping stage of a hydrocarbon journey.
“I am at ease in the desert,” says Fadly, who joined Shaybah in 2015 after completing Aramco’s industrial training program.
“Before Aramco, my father taught me how to drive in the desert, and in six years at Shaybah, I have never been stuck in the sand,” he adds proudly.
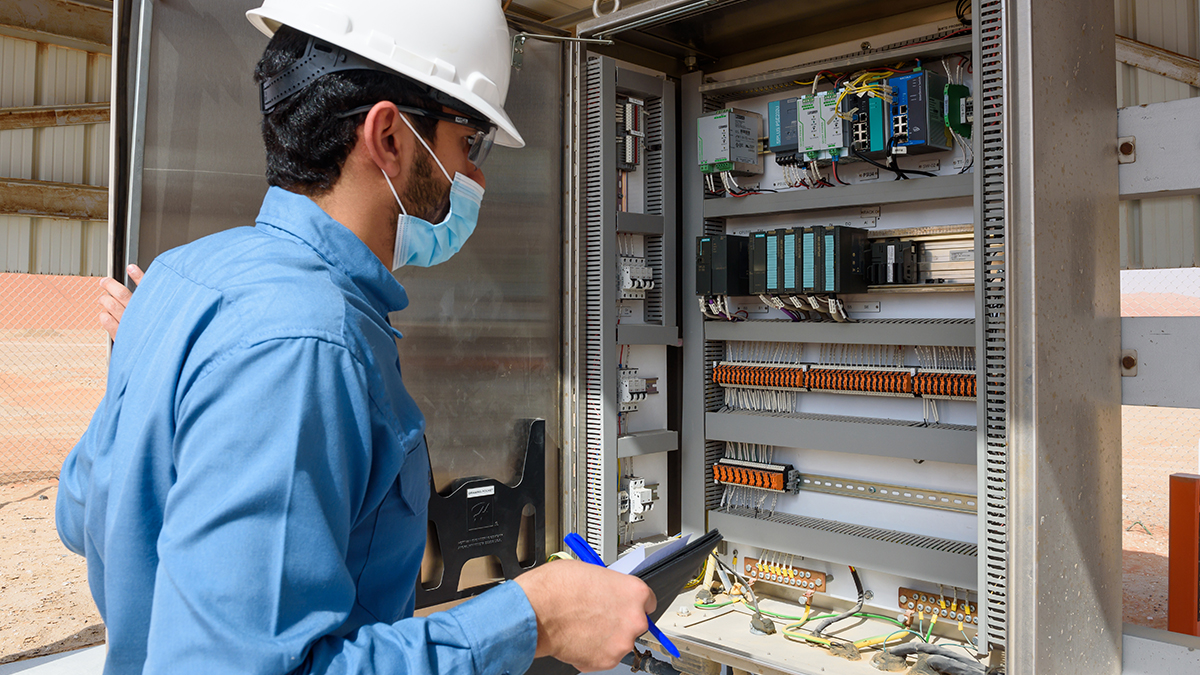
Hydrocarbons on the move
Aramco uses a vast pipelines network to transport hydrocarbons from place to place. They connect the company’s products to multiple facilities for processing or refining, as well as to domestic customers, or export terminals.
It is a decades-old business practice for Aramco to use detection and preventative maintenance to uphold pipeline integrity. Diligent care of pipelines is good for both the business and the environment.
Plus, maintaining smooth-running pipes is a key action toward greenhouse gas (GHG) emission mitigation.
Three pipelines
Stretching to Fadly’s north, as he begins his routine check of “kilometer 9.8,” three pipelines head into the deep golden vastness.
Two are 46- and 30-inch underground carbon steel pipelines that stretch 645 km to carry crude oil through the Rub’ al-Khali desert to the oil and gas industrial heartland of Abqaiq.
Running parallel to the two crude pipelines, also underground, is a 36-inch pipeline containing natural gas, compressed into liquid form, or NGL.
Spaced about 100 km apart and equipped with sophisticated instruments are remote terminal units.
The units transmit the pipeline’s flow, pressure, and temperature parameters to Aramco’s operational nerve center, the Oil Supply Planning and Scheduling Department (OSPAS), located in the company's Dhahran headquarters.
Pipelines connect the company’s products to multiple facilities for processing or refining, and to domestic customers, or export terminals.
Humanity and technology united
One of the world’s largest oil fields, Shaybah’s production approach combines advanced technology and Aramco’s decades-old approach to diligence. As an example, Fadly points to yellow triangle navigational markers located every 1 km on the main pipelines.
“Plus, we have many sensors at precise locations, checking every hour of every day for leaks and failures,” he says.
Fadly’s check of “kilometer 9.8” starts with the perimeter fence and progressively works its way around the junction’s equipment. Gauges measuring pressure and temperature, as well as electronic sensors, monitor the NGL pipeline and its safety bypass line.
OSPAS collects data from thousands of remote terminal units from all company facilities, including pipelines. Its staff can spot any anomaly and execute a host of rectification actions within a few minutes.
“There are many devices feeding data,” says Fadly. “If an alarm goes off here, OSPAS knows.”
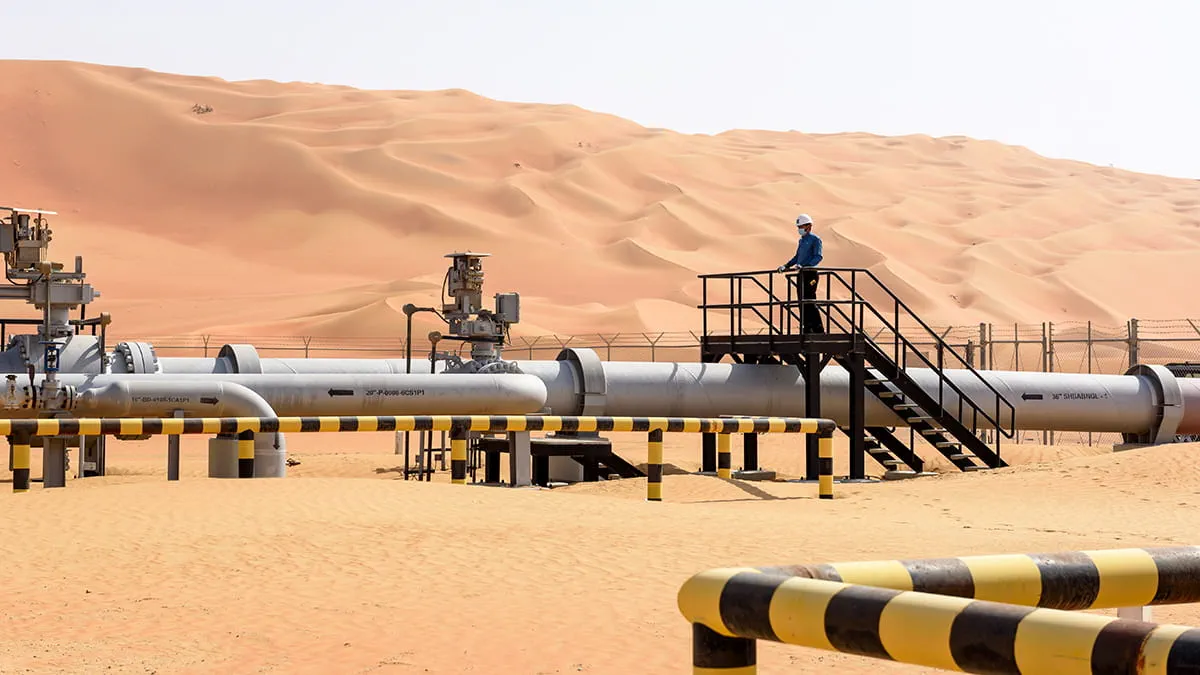
Renewing to save crude
Using renewable energy minimizes GHG emissions and saves precious hydrocarbon resources for better economic use.
Aramco deploys renewable energy systems in its office buildings and industrial facilities, and the company installed the Kingdom’s first wind turbine at Turaif Bulk Plant in January 2017.
At Shaybah’s 26 main pipeline junctions, solar panels power the valves, lighting system, remote terminal unit, and other equipment. Meanwhile, the cathodic protection system’s electrochemical cell has its own solar panel, so the pipeline’s corrosion can be absorbed into an anode.
“Keeping the pipelines flowing smoothly is best for the environment,” said Fadly. “The planet belongs to all of us, and we have to maintain it in a good way that will not cause damage.”
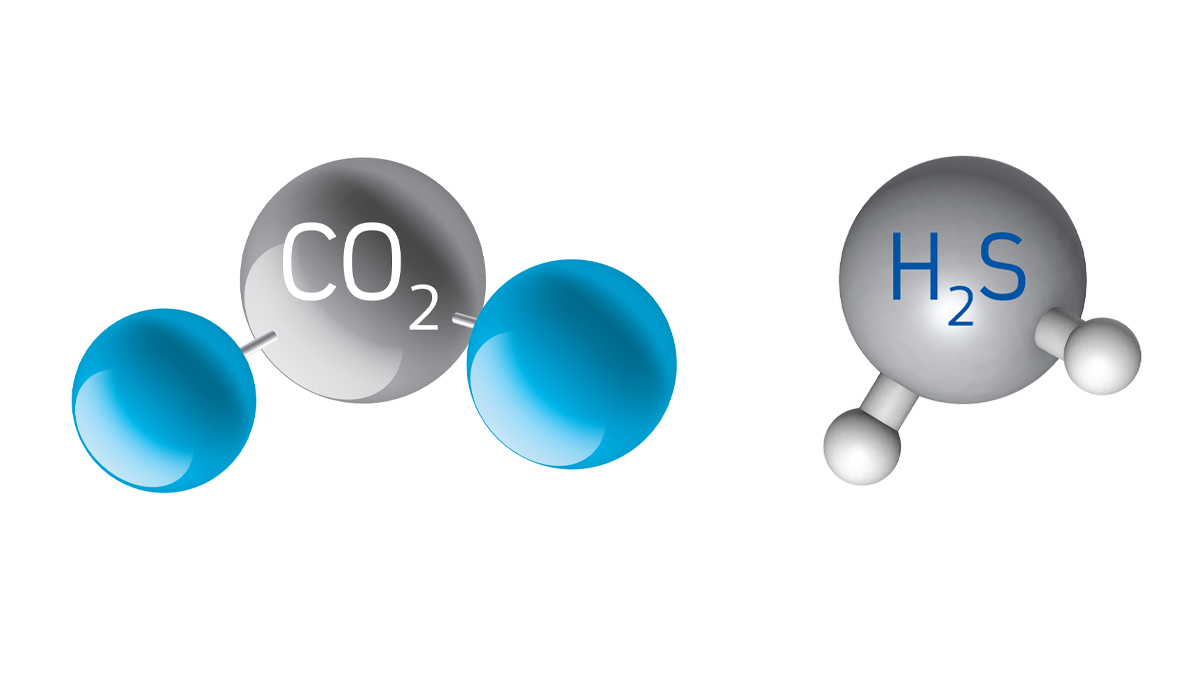
Piping the circular carbon economy
Shaybah’s gas-oil separation plants send the rich gas separated from the crude oil to the site’s natural gas liquid (NGL) recovery plant.
After removing high-value natural gas liquids, the NGL plant recompresses the leftover hydrogen sulfide (H2S), carbon dioxide (CO2) and residual gas, and pipes it for reinjection into the reservoir.
This not only helps to reduce greenhouse gas emissions to the atmosphere, but also helps maintain the reservoir’s pressure.
Injection, usually with water, is one way to give the natural pressure of a reservoir a helping hand, but water is scarce in Shaybah’s desert location.
Returning leftover gas to the reservoir is a win-win for the environment and business.
Without pipes, none of this would be possible.
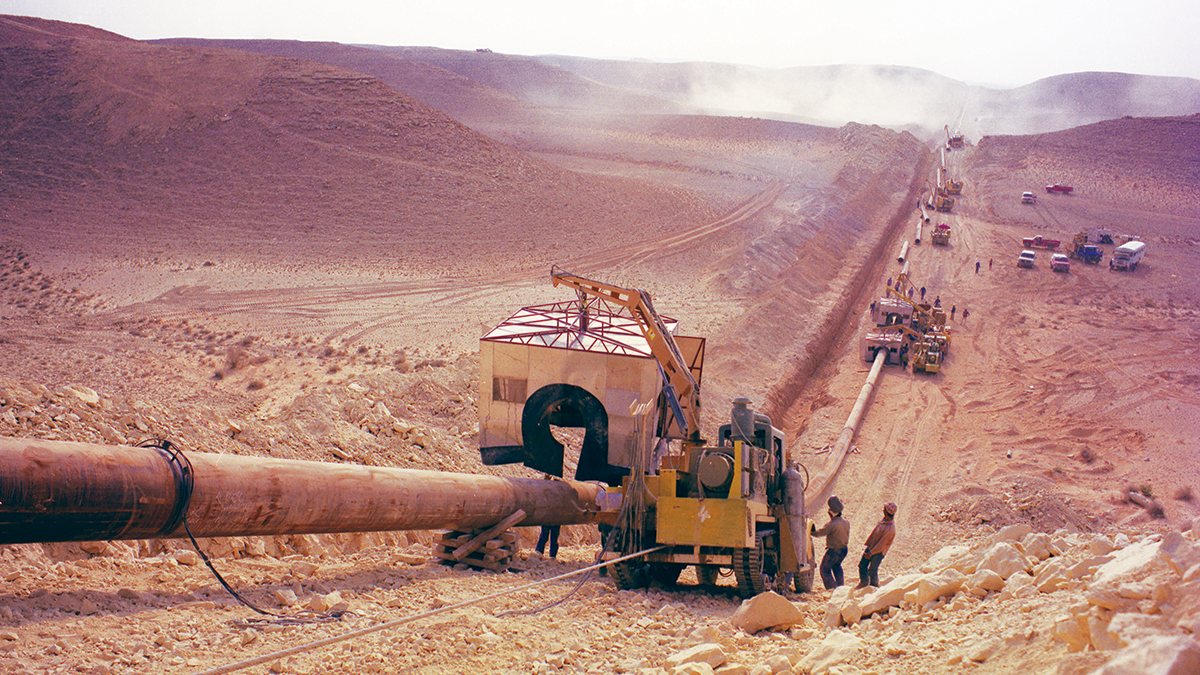
Transporting hydrocarbons
First-class operational standards are behind Aramco’s low carbon intensity, and extensive cross-Kingdom pipelines safely and quickly move the oil, natural gas, and natural gas liquids (NGL) that Aramco produces.
Major cross-country pipelines include the Saudi Arabia–Bahrain Pipeline, as well as the East-West Crude Oil, natural gas, and NGL pipelines to Yanbu‘ on the Red Sea.
The NGL pipeline linking Yanbu‘ and Shedgum was the longest and most advanced gas line ever built at 1,170 kilometers.
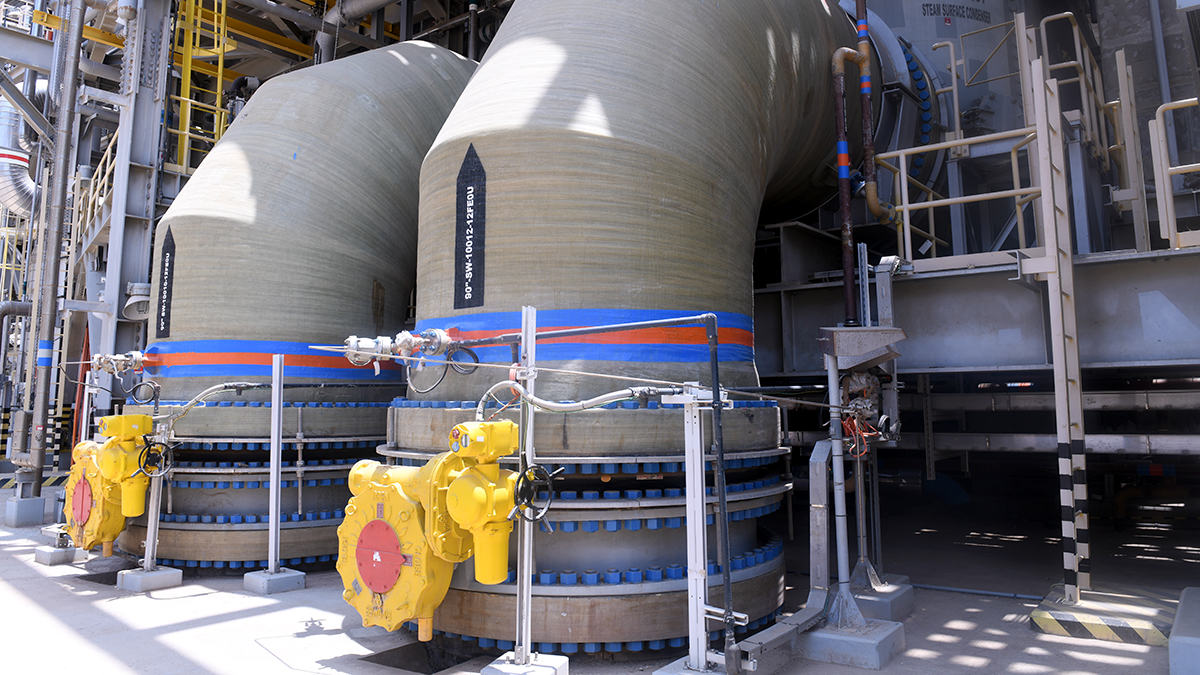
Smarter pipeline thinking
Corrosion is a worldwide problem, with its global cost is estimated at $2.5 trillion.
Common oil field fluids, H2S, CO2, and even bacteria cause corrosion and compromise pipeline integrity, safety, and reliability over time.
Corrosion management — inspection, detection, correction, and prevention — reduces corrosion’s risks and costs.
Nonmetallic pipes, resistant to corrosion, are flowing a new future for oil production pipelines.
These advanced durable materials (lighter than their conventional counterparts) successfully control corrosion and have been used in most Aramco facilities for more than two decades.
To research nonmetallic technologies, Aramco opened a Nonmetallic Innovation Center outside Cambridge University, U.K., in 2019.