Global September 14, 2021 - By
At Shaybah, decades of greenhouse gas mitigation is in our operational DNA.
A proverb counsels, “There are no short cuts to any place worth going.”
Every work shift, foreman Yasser Y. Hakami and his front-line colleagues diligently apply this wisdom to systematically care for one of the Shaybah oil field’s four gas-oil separation plants (GOSP).
Hakami says cutting corners is never an option for the smooth operation of a GOSP — the first stage of crude oil’s separation into gas, oil, and water.
“We have set monitoring routines, which we continually repeat to take care of the equipment, to keep our people safe, and to minimize our environmental footprint,” he explained.
Our job is to be careful and meticulous so issues are caught and resolved early, before they could turn into a bigger problem.
— Yasser Y. Hakami
“We stop fugitive greenhouse gases leaking into the environment because we inspect the equipment to catch them before they leak,” said Hakami, who has worked at Shaybah for 16 years.
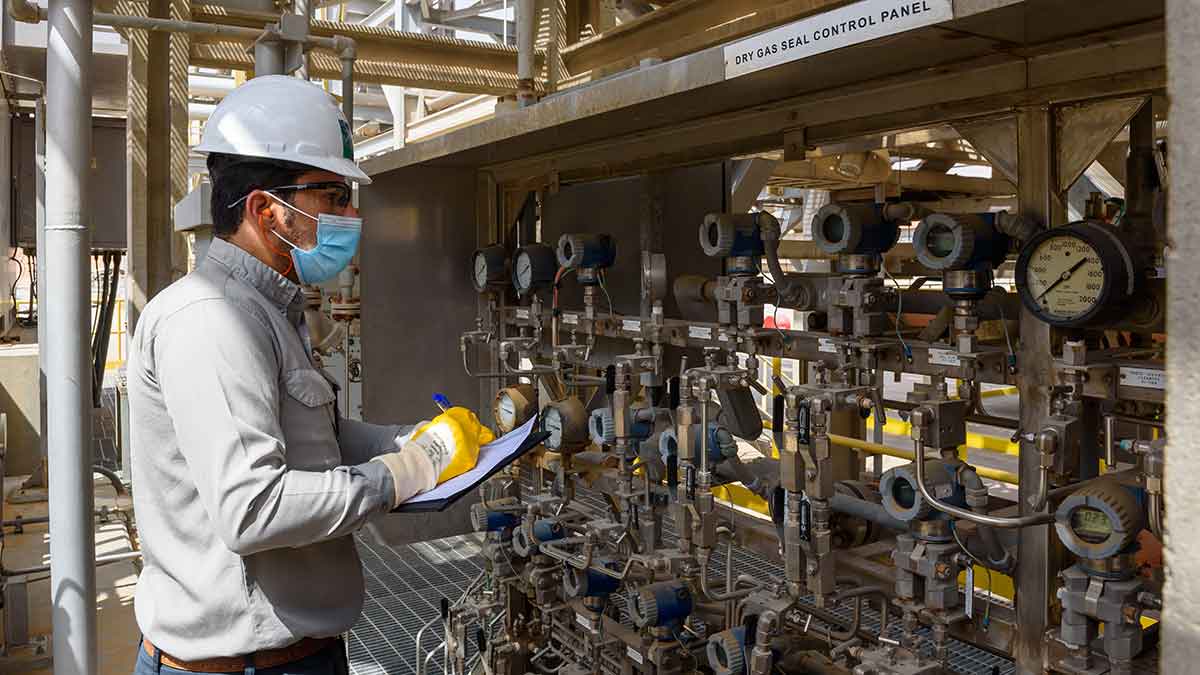
Flowing production chains are cleaner
After crude oil is extracted from the wellhead it journeys through an underground trunk line pipe to a GOSP.
On this leg of a hydrocarbon’s journey, keeping the crude oil running smoothly, and safeguarding against leaks of invisible gas, are key greenhouse gas (GHG) mitigation measures.
Separation is when a gas-oil separation plant uses depressurization to perform the initial processing of crude oil, separating wellhead fluids into constituent vapor (gas) and liquid (oil and produced water).
Sources of equipment leaks include valves and seals for pumps, connectors such as flanges and fittings used to join piping and process equipment, seals on compressors, and valves for pressure relief devices.
The wet crude’s first stop at the steel forest is a three-phase separator, known as a “high-pressure production trap,” where gravity separates the oil from the gas and water. While the off-gas goes to the gas gathering system, the oil goes for further water and salt removal, before the treated crude is sent to a stabilization plant for further processing.
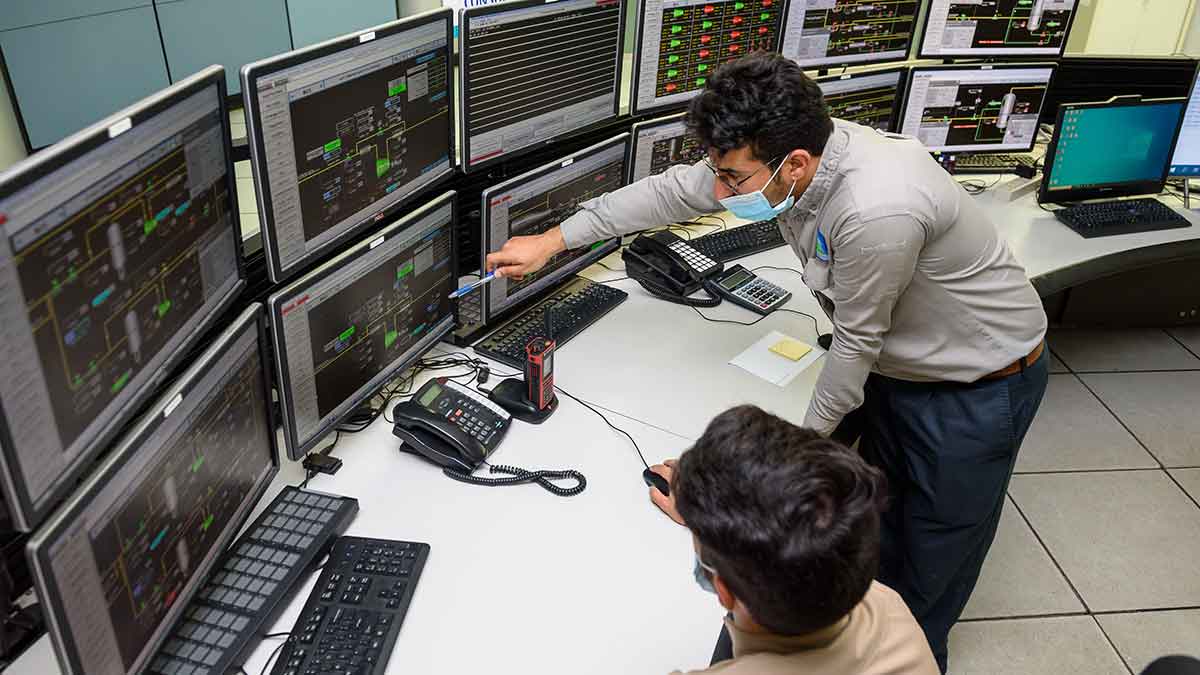
Human and digital eyes checking
Working in tandem with technology makes for a lower carbon, more efficient, and safer operation.
Technology and humans connect to maintain the 24/7 operational hum of a GOSP.
At the start of Hakami’s 12-hour GOSP shift, he completes a checklist of the pipes, vessels, pumps, compressors, and other equipment.
It’s a rigorous process, seeing him methodically record many gauge readings. In four hours, he repeats the process — and, after the following four hours, he does it again.
Meanwhile, giving Hakami a helping hand are numerous sensors tirelessly feeding a multitude of electronic readings into the plant’s digital heart, the central control room. Inside the nerve center, data readings are used to monitor, predict and diagnose. With just the touch of a button, equipment can be stopped, started, or flows and pressures reduced or increased.
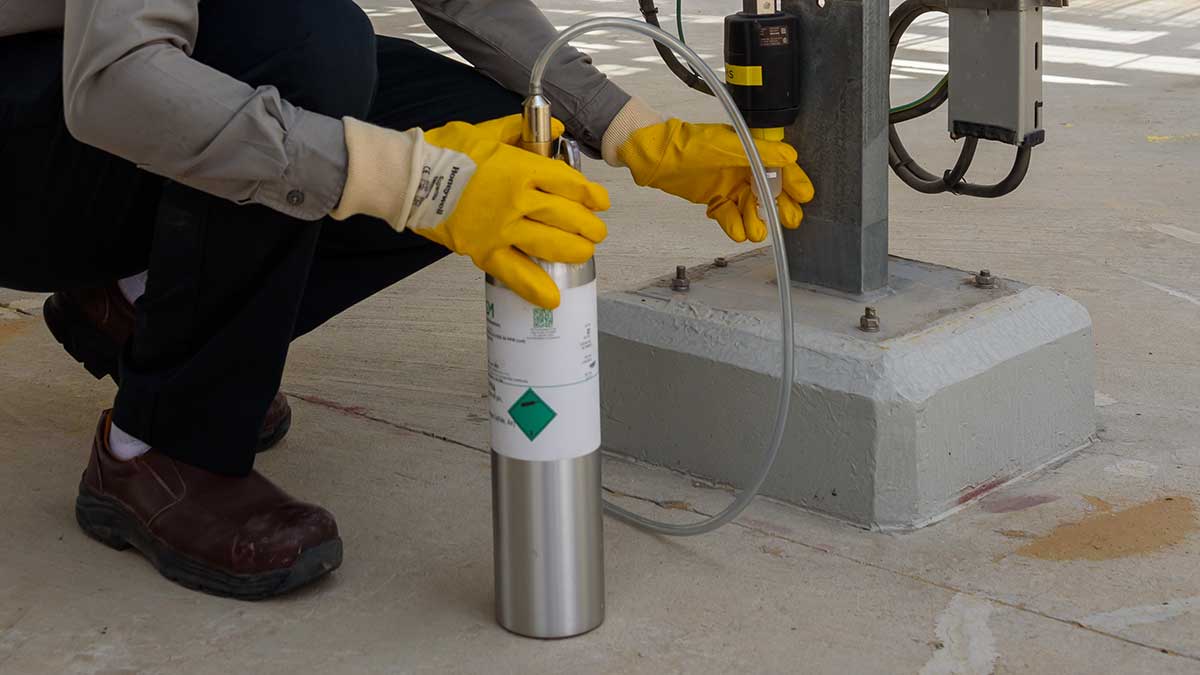
Maintaining critical paths
Aramco manages the world’s second largest crude oil reserves, and invests in the lowest carbon production to maintain its critical paths.
Inherent to oil and gas work are safety and environmental risks, and for GHG mitigation, a steady heartbeat for the crude oil production chain is best.
The company’s apprenticeship program prepares its operators for the production forefront, and GOSP teams are trained specialists in production separation.
Their passion is following procedures — procedures which protect the environment from traveling to place where no one wants it to go.
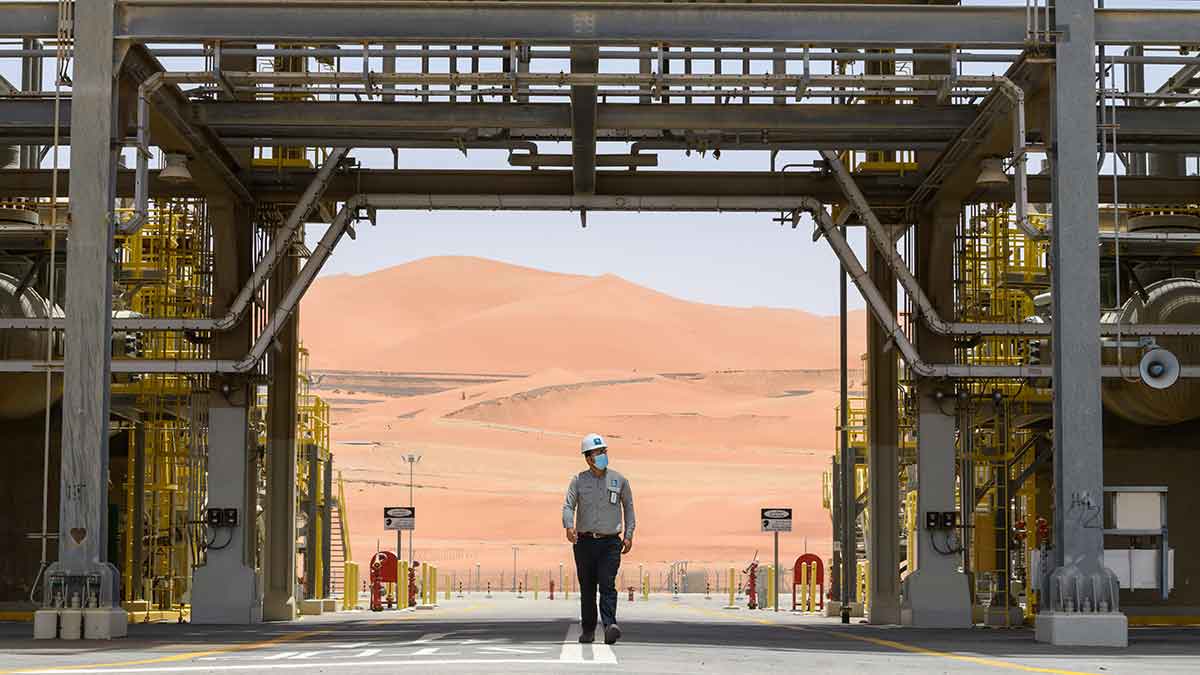
Shaybah oil field
Shaybah is on the northern edge of the largest uninterrupted desert expanse in the world, and is one of the world’s largest oil fields.
From four GOSPs, a gas compression plant, power generation plants, and water desalination facilities, the facility produces highly valued sweet Arabian Light, and Extra Light oils, which are virtually sulfur-free, and high in their gasoline fraction.
Mesmerizing mountainous reddish-brown sand dunes constantly move in its unforgiving arid climate, where temperatures reach 50 degrees Celsius in summer, and fall to near freezing in winter.
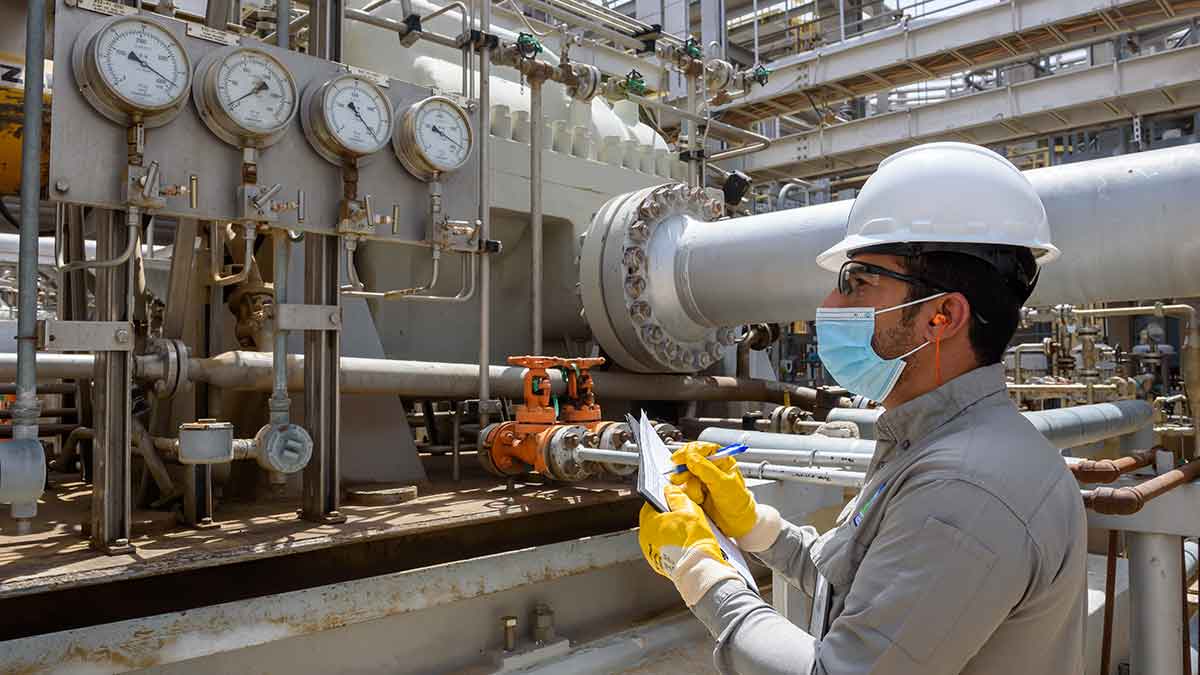
Moving treated crude
Oil pumps at the Shaybah GOSPs move treated crude into a 645-km northern pipeline, where it travels by the force of gravity to the world’s largest crude oil stabilization facility, Abqaiq.
Foreman Yasser Y. Hakami describes his role as providing unity to the GOSP, “I look out for everything, for employees, the gas detection system, the integrity of the plant equipment, and the safety equipment.”
Thanks to the company’s pipeline detection equipment, he has never had to work with a pipeline crack.
“A leakage of crude is bad for the environment and the worker,” said Hakami. “But, if there was a leak, our instant safety shutdown system stops damage to the environment.”
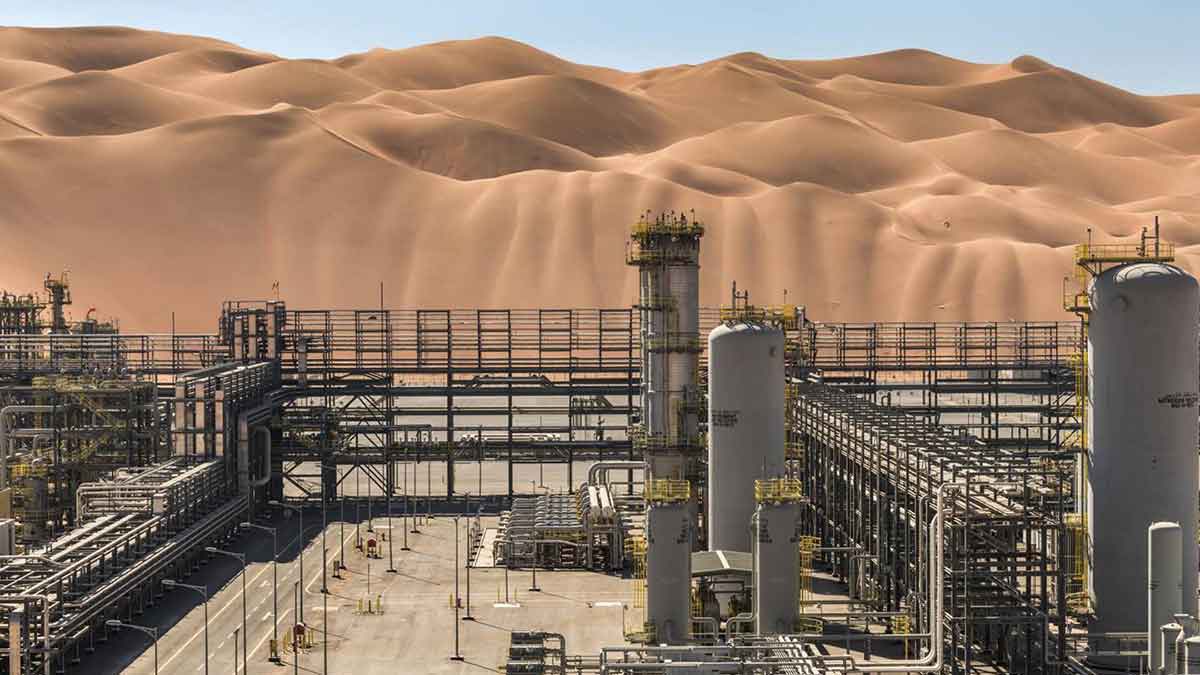
Shaybah NGL enhanced oil recovery
At Shaybah, gas from the wet crude — associated gas — is sent by the gas compressor to the nearby Shaybah natural gas liquid recovery plant.
The plant recovers high-value natural gas liquids, such as propane, butane and ethane, which it pipes to Ju’aymah and Yanbu’.
To further reduce emissions, the leftover gas — hydrogen sulfide and carbon dioxide — is recompressed, and reinjected into the Shaybah reservoir for enhanced oil recovery.